In the world of electrical engineering, particularly in the operation of three-phase induction motors, the star-delta connection is a critical concept. This configuration is essential for starting motors efficiently and reducing electrical stress. In this blog, we’ll explore why star-delta connections are used, how they work, and the process of applying them.
What is a Star-Delta Connection?
A star-delta connection is a method used to start a three-phase induction motor. It involves initially connecting the motor windings in a star (Y) configuration and then switching to a delta (Δ) configuration once the motor reaches a certain speed.
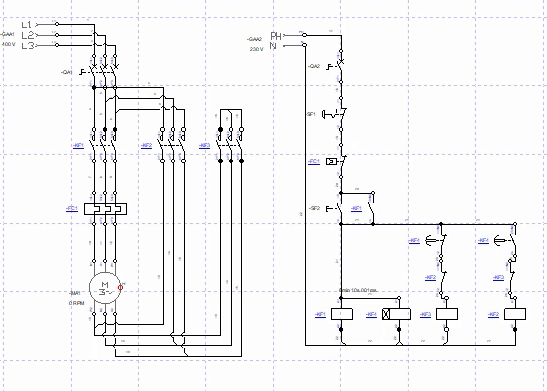
Why Use a Star-Delta Connection?
Reduced Starting Current:
When a motor starts in a star configuration, the voltage across each winding is reduced to 1/√3 (approximately 0.577) of the line voltage. This reduces the starting current to about 1/3 of what it would be if the motor started directly in delta configuration.
By limiting the starting current, the star-delta method helps in avoiding high inrush currents which can cause electrical and mechanical stress.
Lower Torque During Startup:
Starting in star reduces the starting torque to about 1/3 of that in delta, which can be beneficial for applications where high starting torque could lead to mechanical damage or excessive load on the system.
Reduced Mechanical Stress:
The gradual increase in voltage from star to delta reduces mechanical stress on the motor and connected machinery, leading to a longer lifespan of both.
How Does the Star-Delta Connection Work?
Star Connection (Y):
In the star configuration, each winding of the motor is connected to a common neutral point. The line voltage applied is split among the windings, thus reducing the voltage and starting current.
The star connection is used during the initial startup phase.
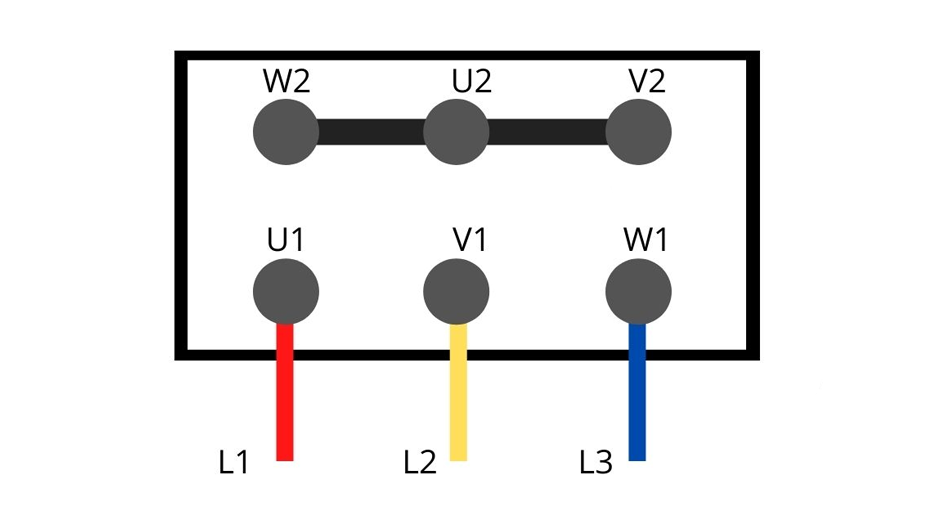
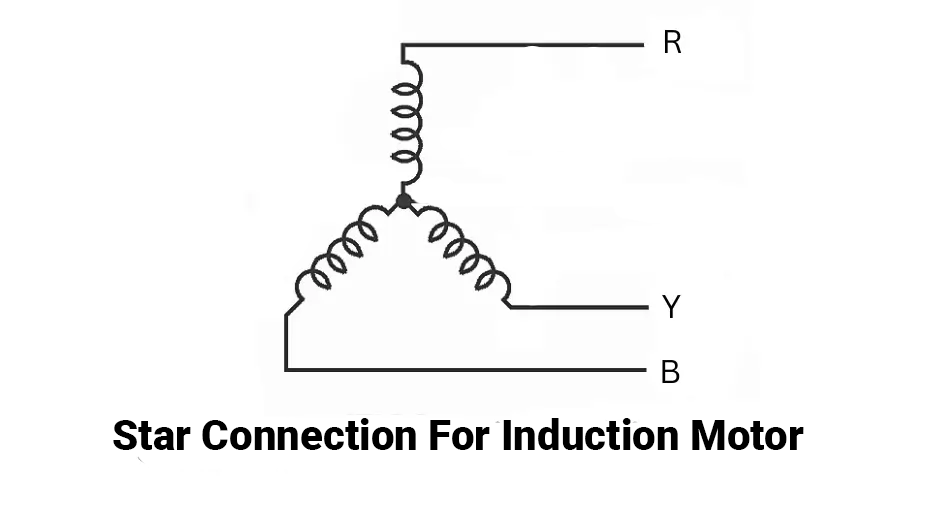
Delta Connection (Δ):
- In the delta configuration, the windings are connected in a loop, and each winding receives the full line voltage. This results in normal operating torque and speed once the motor has reached a certain speed.
- After the motor reaches approximately 70-80% of its rated speed, the connection switches to delta.
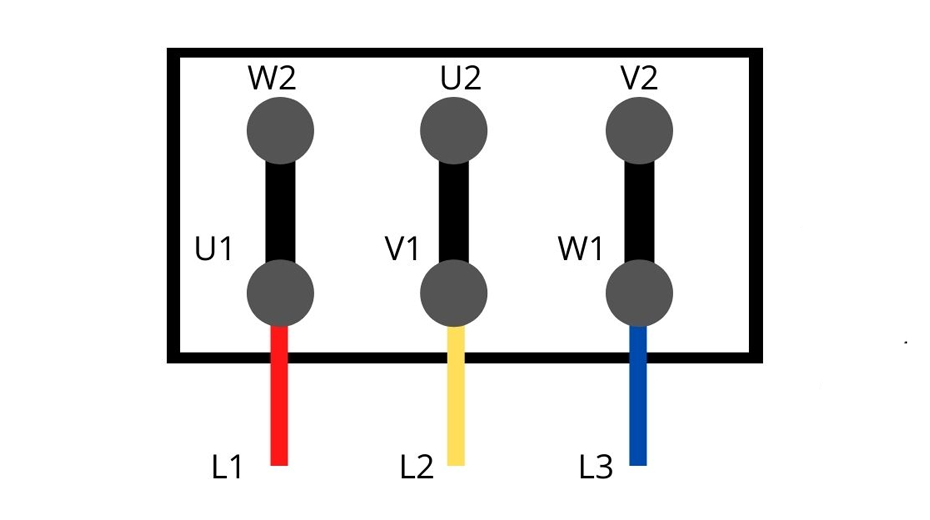
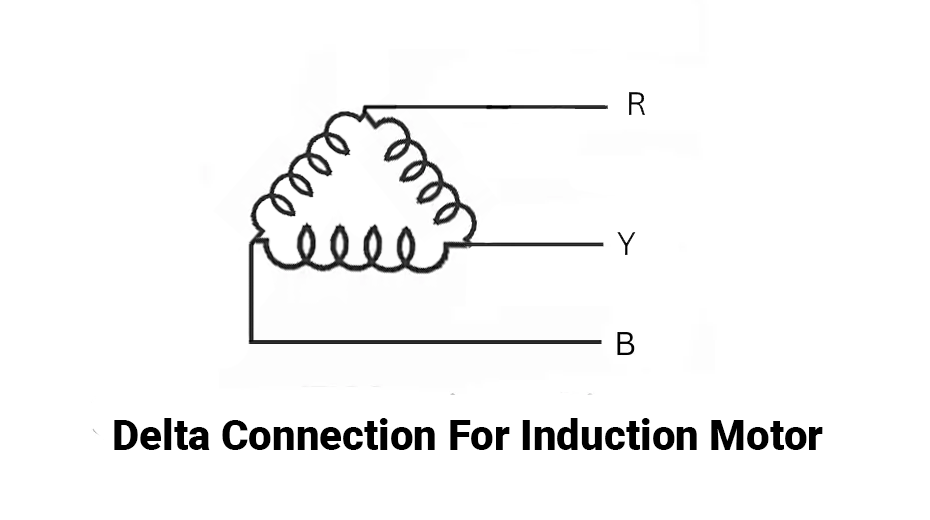
Steps to Apply a Star-Delta Connection:
Initial Setup:
Ensure that the motor and control panel are properly rated for star-delta starting. Install a star-delta starter, which includes a star contactor, a delta contactor, and a timer.
Wiring the Motor:
Connect the motor windings in a star configuration initially. This involves connecting each phase to a common neutral point and then connecting these to the power supply through the star contactor.
Switching to Delta:
Set up a timer in the control panel to switch the motor windings from star to delta once the motor has reached the desired speed. The delta contactor should engage while the star contactor disengages.
Testing and Adjustment:
Test the system to ensure that the transition from star to delta is smooth. Adjust the timer settings if necessary to ensure optimal performance and avoid excessive starting current.
Monitoring:
Continuously monitor the motor for any unusual vibrations, noises, or overheating. Proper maintenance and timely adjustments can enhance the reliability of the star-delta starting system.
Benefits and Drawbacks
Benefits:
- Reduced starting current helps in preventing voltage drops in the power supply system.
- Lower mechanical stress on the motor and connected machinery during startup.
Drawbacks:
- Requires additional components such as contactors and timers, which add to the initial cost.
- Not suitable for all types of motors, particularly those that require high starting torque.
Conclusion
The star-delta connection is a practical and efficient method for starting three-phase induction motors. By reducing the starting current and mechanical stress, it contributes to a more stable and longer-lasting motor operation. Understanding how to apply this connection correctly can greatly benefit both the performance and longevity of your motor system.
By implementing a star-delta starter, you can ensure a smoother startup process, reduce electrical and mechanical strain, and achieve better overall efficiency in your motor-driven applications.