When dealing with three-phase induction motors, one crucial decision is choosing between star (Y) and delta (Δ) connections. These configurations significantly impact the motor’s performance, starting characteristics, and overall efficiency. In this blog, we’ll explore the differences between star and delta connections, including their voltage and current relationships, starting and running characteristics, applications, and more.
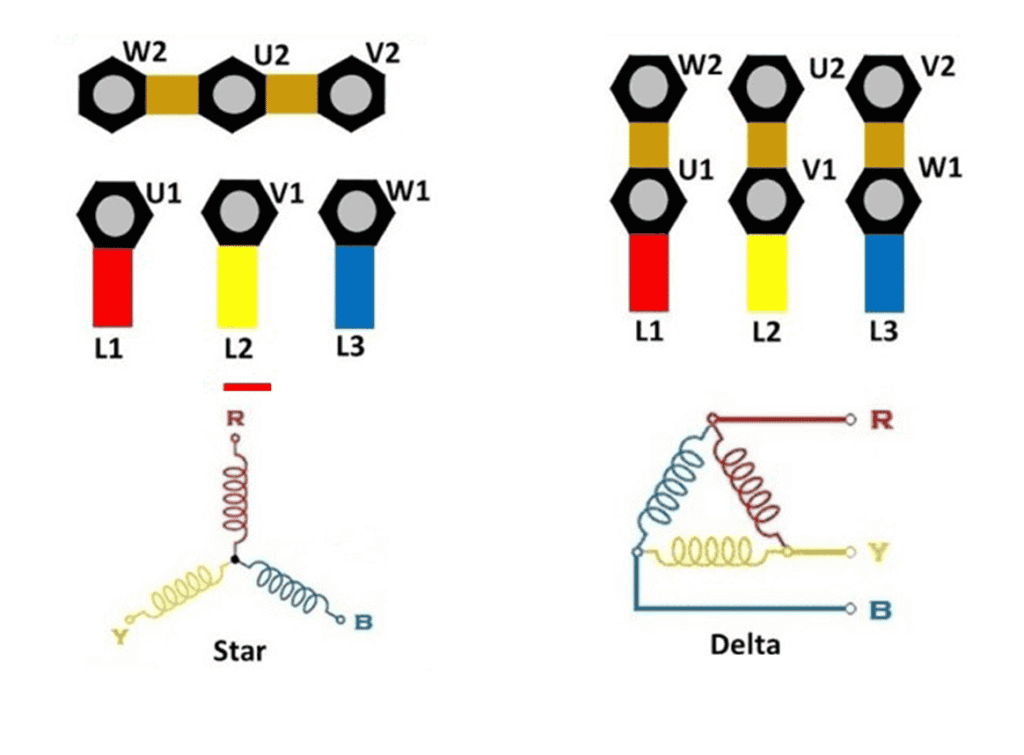
What Are Star and Delta Connections?
Star Connection (Y Connection)
In a star connection, one end of each of the three windings of the motor is connected at a common point, called the star point. The other ends are connected to the three phases of the power supply. This configuration creates a “Y” shape.
Delta Connection (Δ Connection)
In a delta connection, each winding is connected end-to-end in a loop, forming a closed triangle. Each corner of this triangle connects to one of the three phases of the power supply.
Voltage and Current Relationships
Understanding how voltage and current behave in star and delta connections is fundamental to their application:
Star Connection
Line Voltage (V_L): The voltage across each winding, known as phase voltage, is equal to
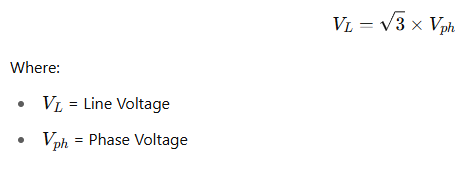
Line Current (I_L): The current through each winding is the same as the line current, is equal to
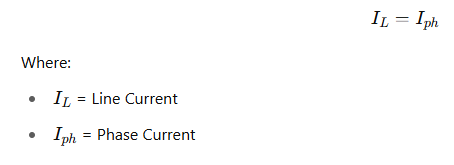
Delta Connection
Line Voltage (V_L): The voltage across each winding is the same as the line voltage,
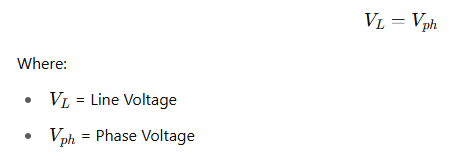
Line Current (I_L): The current through each winding is
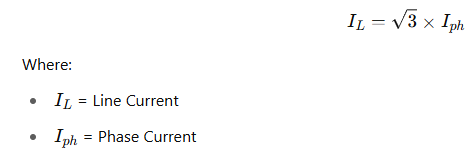
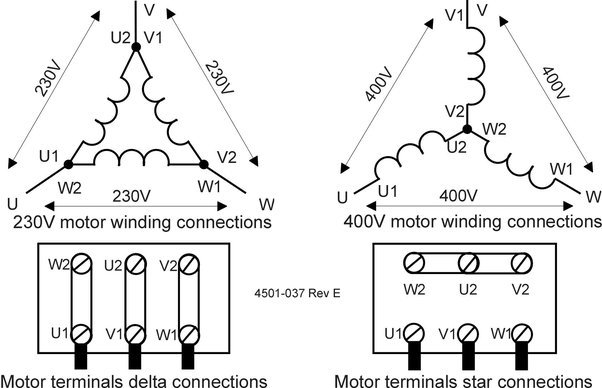
Starting Characteristics
Star Connection
- Starting Current: A star connection limits the starting current because the phase voltage is lower. This is particularly useful in reducing inrush current during motor startup.
- Starting Torque: The torque produced during startup is lower in a star connection due to the reduced phase voltage.
Delta Connection
- Starting Current: The starting current is higher in a delta connection because the full line voltage is applied across each winding.
- Starting Torque: The torque is higher in a delta connection during startup due to the higher phase voltage.
Running Characteristics
Star Connection
- Voltage: After the motor reaches a certain speed, it is often switched to a delta connection to operate at its full rated voltage.
- Torque and Efficiency: Operating in star connection is less efficient for high power output. The torque produced is lower compared to the delta connection.
Delta Connection
- Voltage: The motor operates at its full rated voltage in delta connection, providing maximum torque and efficiency.
- Torque and Efficiency: The motor produces higher torque and operates more efficiently in the delta connection.
Applications and Switching
Star Connection
- Applications: Ideal for starting, as it reduces starting current and torque. Often used in a star-delta starting method to manage high starting currents.
- Switching: Typically used during the startup phase, after which the motor switches to delta connection for normal running.
Delta Connection
- Applications: Best suited for continuous running where high torque and efficiency are required.
- Switching: Used during normal operation to achieve full load performance.
Power Factor
Star Connection
Usually has a lower power factor compared to delta connection due to the reduced voltage across the windings.
Delta Connection
Generally provides a higher power factor, improving the motor’s overall efficiency.
Complexity and Cost
Star Connection
- Cost: May involve additional costs for a star-delta starter switch or relay.
- Complexity: Requires a star-delta starter for switching, adding complexity but managing starting currents effectively.
Delta Connection
- Cost: Typically simpler and potentially cheaper for applications that don’t require a starting switch.
- Complexity: Simpler operation when running continuously.
Final Words
Choosing between star and delta connections for a three-phase induction motor is crucial for optimizing performance and efficiency.
- Star Connection: Ideal for the starting phase to limit current and reduce initial torque. Commonly used with a star-delta starting method to manage high inrush currents.
- Delta Connection: Best for running conditions, providing higher torque and efficiency once the motor reaches its operating speed.